In Sage X3, we may come across a scenario where we need to calculate machine and labor time for the specific release quantity on basis of time, cost for machine and labor will be calculated.
Navigate to -> Manufacturing -> Technical Data -> Standard Operation
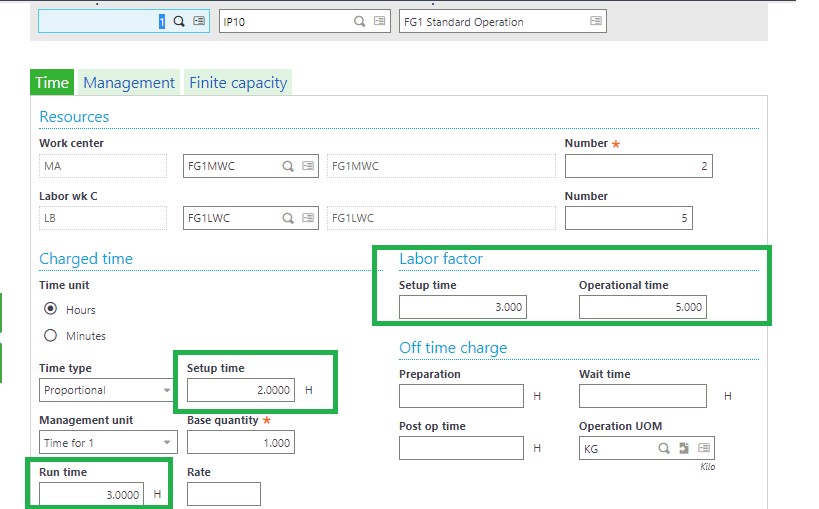
- Here we have entered setup and run time for machine is 2 & 3 hours respectively.
- And we have entered setup and operational time for labor is 2 & 5 hours respectively.
- There is no impact of preparation, wait time and post operation time on cost calculation.
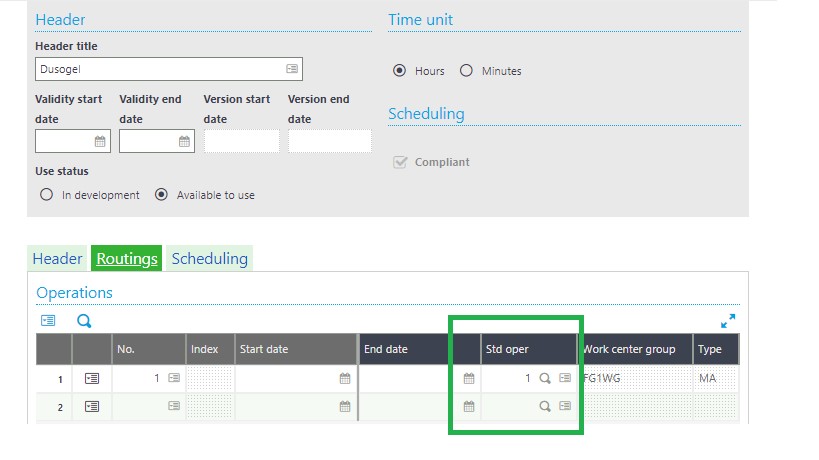
- We need to map standard operation in routing management so that it can invoke the details (Work centers, operational timings, etc) in routing management.
- Routing code is tagged with finished good product so it will be directly inherited in work order and calculation will be as per standard operation.
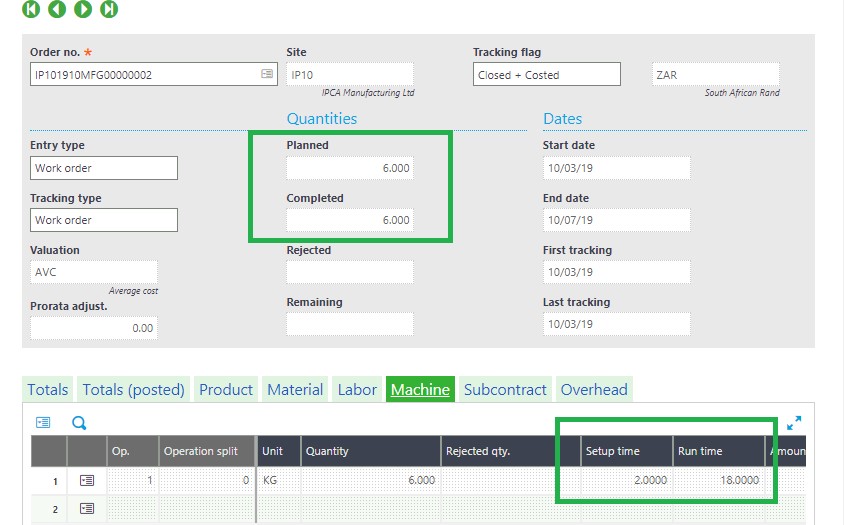
- Now for a completed work order for release quantity 6, calculation will be as follows.
- Machine:
Declaration in standard operation
Setup Time: 2 Hours
Run Time: 3 hours / UN
Calculation for work order
Setup Time: 2 hours
Run Time: 3 Hours / UN * 6(release Quantity) = 18 Hours (Total for work Order)
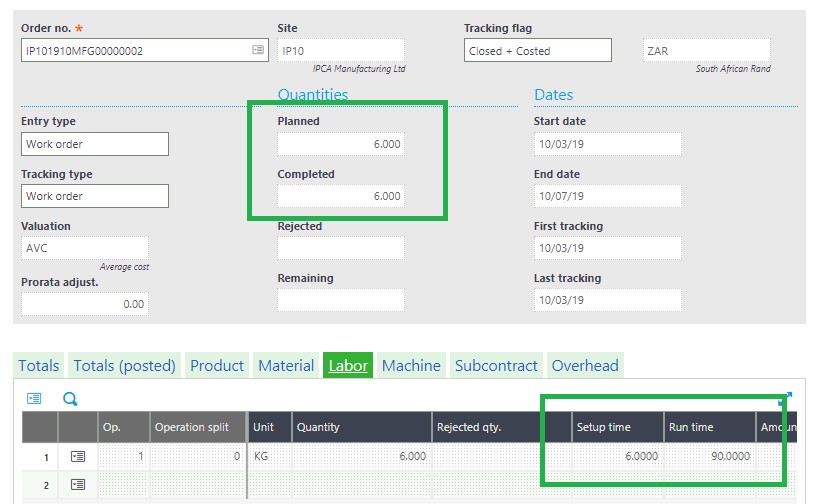
- Labour:
Setup Time: 2 Hours
Operation Time: 5 hours / UN
Calculation for work order
Setup Time:
2 hours (Machine Setup Time) * 3 hours (labour Setup Time) = 6 Hours
Operational Time:
3 Hours (Machine Run Time) * 6 (release Quantity) * 5 Hours (Operational Time) = 90 Hours (Total for work Order)
- On basis of calculated time, final cost will be calculated.